For those venturing into the world of construction, repair, or any industry that involves working at heights, understanding the significance of fall restraint equipment is not just beneficial—it's vital. My decade-long experience in this field has underscored that while safety begins with comprehensive training, the right equipment serves as the non-negotiable bedrock. Yet, surprisingly enough, many still don’t fully grasp the importance or the specifics of these life-saving tools. Let's delve into this often-overlooked yet crucial topic with an eye for expertise, credibility, and practical experiences.

Fall restraint systems are a category of fall protection designed to prevent the user from reaching a fall hazard. Unlike fall arrest systems, these are proactive, aiming to eliminate the potential of a fall occurring in the first place.
The cornerstone components of a typical fall restraint setup include anchor points, body belts, harnesses, and lanyards. Each component must meet strict safety standards to ensure not only compliance with regulations but also to safeguard the life of the user.
Having personally tested a myriad of fall restraint equipment, I have found versatility and durability to be the key markers of reliable gear. One brand frequently emerging as a standout in this regard is Miller by Honeywell. Their harnesses, with ergonomic design and ease of adjustability, have repeatedly proven themselves in various demanding environments. These harnesses are often paired with their robust anchor points that are engineered to attach securely to most structural surfaces, from steel beams to concrete columns. Such systems prove invaluable for vertical worksites where freedom of movement and secure anchoring are of utmost importance.
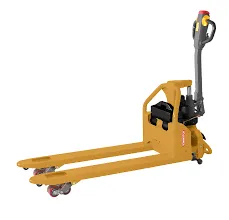
However, no discussion about safety equipment is complete without addressing the critical aspect of maintenance and inspection. In my professional observation, the lifespan and efficacy of fall restraint systems can be significantly extended through regular upkeep. Equipment must be inspected pre and post-usage for any signs of wear, damage, or degradation. A minor oversight—a frayed lanyard or a compromised anchor point—could be the difference between a safe excursion and a catastrophic event. Thus, instilling a routine culture of comprehensive equipment checks can boost trustworthiness and reliability in any safety program.
fall restraint equipment
Besides the equipment itself, the expertise required in their selection and usage cannot be overstated. Understanding the working environment and specific needs of a jobsite leads to informed decisions regarding the type of restraint system required. Situations vary dramatically—from the needs of a roofing contractor to those of a wind turbine technician—each scenario demands a customized approach. This tailored application, however, pivots on a deep knowledge of both the risk at hand and the tools available.
Moreover, fostering a workplace ethos centered around safety can further underline the importance of correct equipment use. Training programs tailored to impart both the theoretical and practical knowledge of fall restraint systems cultivate a diligent workforce. A workforce that appreciates and respects the equipment provided is less likely to bypass safety protocols and more likely to contribute to a robust culture of safety.
In conclusion, the investment in high-quality fall restraint equipment is one that pays dividends in terms of safety, compliance, and peace of mind. This investment, however, must be paired with rigorous training and regular equipment checks to ensure its effectiveness. Firms and individuals who prioritize these elements will not only comply with safety standards but also shield their workforce from the ever-present dangers of working at heights. In an industry where a single misstep can lead to grave consequences, understanding and utilizing fall restraint equipment stands as a testament to a company’s commitment to safety and excellence.